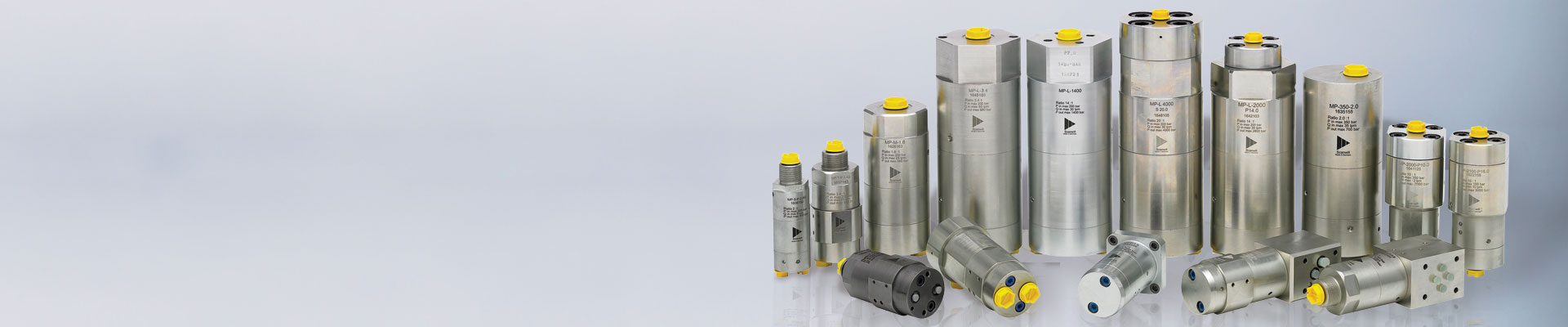
BLOG
IC-Fluid Power brings the world to you by sourcing off-the-shelf and custom hydraulic components from around the globe.
From in-depth case studies highlighting the real-world applications of hydraulic products to solution-driven, informative blogs that tackle industry pain points, IC-Fluid Power is your go-to hub for all things hydraulics. We offer a wide range of knowledge, including insights that empower professionals and enthusiasts alike to stay ahead in this tried and true, but still evolving, field.
We aim to provide fresh, relevant content that explores the many facets of the hydraulics industry and its trusted, loyal community. Whether you’re seeking innovation, practical advice, or a deeper understanding of trends and technologies, IC-Fluid Power’s blog is here to connect you with the information and stories you may need.
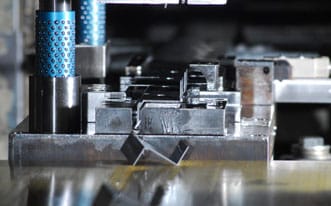
Shock Dampers for Snap Through
Shock dampers are one of the best kept secrets of the metal stamping industry. Many people have heard of them… Read More »Shock Dampers for Snap Through
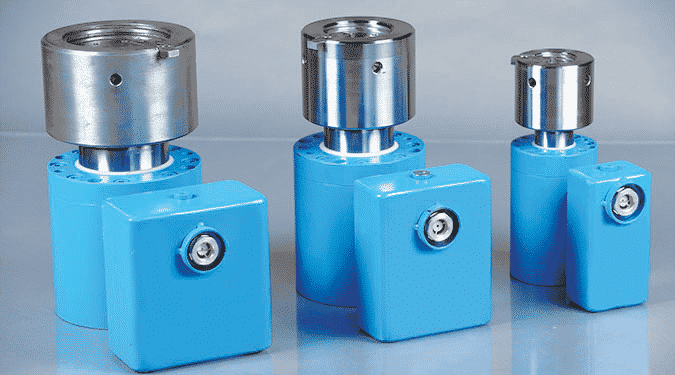
Case Study: SKD Automotive Group | Hylatechnik Shock Dampers
Founded in 1937 and based in Troy, Michigan, SKD Automotive Group manufactures and supplies metal stampings, components, and weldments to… Read More »Case Study: SKD Automotive Group | Hylatechnik Shock Dampers
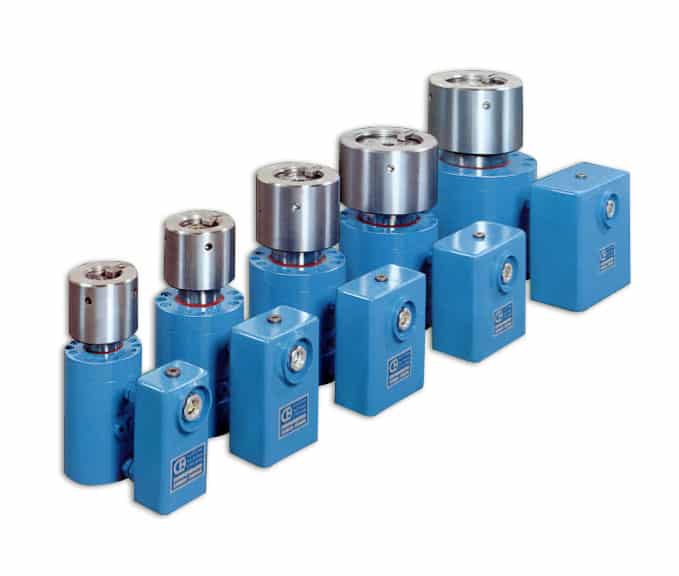
Reverse Tonnage Reduction with the Use of Shock Dampers
Hydraulic shock dampers can be beneficial to reduce the effects that come from reverse tonnage. This device can reduce wear… Read More »Reverse Tonnage Reduction with the Use of Shock Dampers