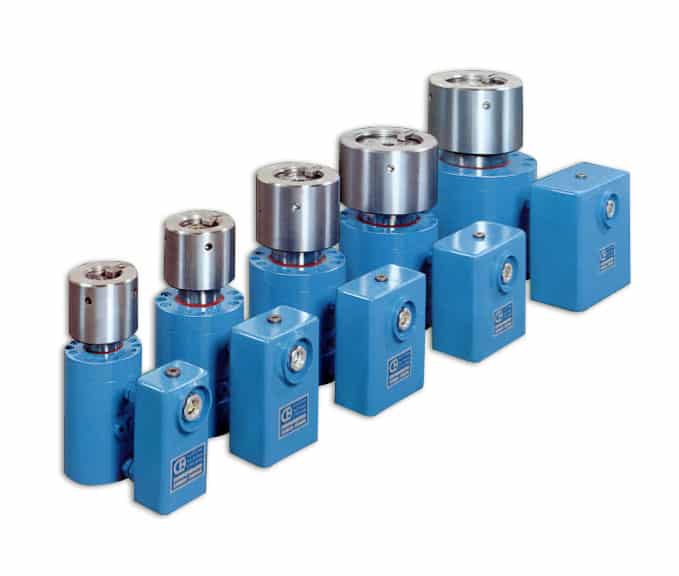
Reverse Tonnage Reduction with the Use of Shock Dampers
Hydraulic shock dampers can be beneficial to reduce the effects that come from reverse tonnage. This device can reduce wear and damage and keep presses working more efficiently and with fewer problems.
The Signs of Reverse Tonnage Problems
Reverse tonnage issues show up over time with many signals. Failure of slide connection area press components can indicate negative tonnage problems. Problems with other frame parts or premature wear of punches and dies can also imply issues with tonnage. Here are some more indicators:
- Loose air and hydraulic lines
- Leaking air and hydraulic lines
- Electrical problems
- Foundation issues
- Extreme high levels of noise
A shock damper can reduce the effects of negative tonnage to prevent these symptoms from occurring. Reverse tonnage is typically seen in blanking applications and cutting and perforating applications.
The press frame will see tension and compression loads with each stroke of the press. If these loads exceed the designed elastic limits of the press, the press frame will be damaged. This type of damage will occur with the excess of forward or reverse tonnage. Cracks can occur in the components, including the slide, crown, drive linkage, and housings. The first indication of problems begins with the most vulnerable parts, including hydraulic lines and bolts. The damage can then progress to other areas. However, a shock damper can absorb those forces to prevent the effects to the presses.
With the right hydraulic shock absorber, smaller presses can handle heavier loads and improve their productivity. Other benefits of choosing the right shock damper for your presses include:
- Reduce maintenance costs
- Reduce stresses on the press along with the tooling and foundation
- Increase die life
- Improve part quality
- Reduce noise of operation
The Benefits of Using a Shock Damper
Though you have several solutions to reducing the effects of reverse tonnage to your presses, a hydraulic shock damper is the most versatile option. It is cost efficient and can be retrofitted to work with used presses. It absorbs the shock without reducing the capacity of the press and only adds minor forward tonnage to the job.
Another benefit that you may not think of is that a shock damper can provide better ergonomics for the operator by reducing vibrations which cause stress to the lower parts of the body. It can reduce the physical fatigue that is often felt after several hours of work.
How Do They Work?
The shock damper is designed to limit the slide speed after material breakthrough. This allows more blanking capacity for each press that uses the hydraulic shock damper system.
A hydraulic shock damper can extend the life of your press by protecting it from damage due to reverse tonnage. This is a cost effective way to protect your equipment and help it work more efficiently.
Read how Hylatechnik shock dampers reduced reverse tonnage by 40%.
Reverse tonnage a problem? Call 1-877-ICFLUID to schedule a demo of Hylatechnik shock dampers.
Recent Blogs
Shock Dampers for Snap...
Shock dampers are one of the best kept secrets of the metal stamping industry. Many people have heard of them… Read More »Shock Dampers for Snap Through
read moreCase Study: SKD Automotive...
Founded in 1937 and based in Troy, Michigan, SKD Automotive Group manufactures and supplies metal stampings, components, and weldments to… Read More »Case Study: SKD Automotive Group | Hylatechnik Shock Dampers
read more