Rotary Actuators — Counterbalance Valve Block
Optional load holding valves for intermediate position holding and over center conditions. Aluminum and steel configurations available.
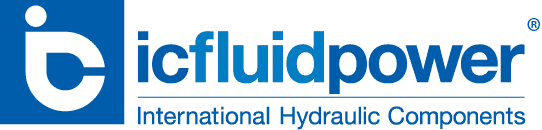
Rotary Actuators – Counterbalance Valve Block
Actuators can be configured with a counterbalance, or load holding valve, to provide load stability and prevent the actuator from reaching excessive torque outputs. Producing back pressure in a hydraulic line gives control over a suspended load to stop unintended motion of the actuator. Valve blocks are available in steel and aluminum, and may be purchased separately if required at a later time. Spare parts are also available.
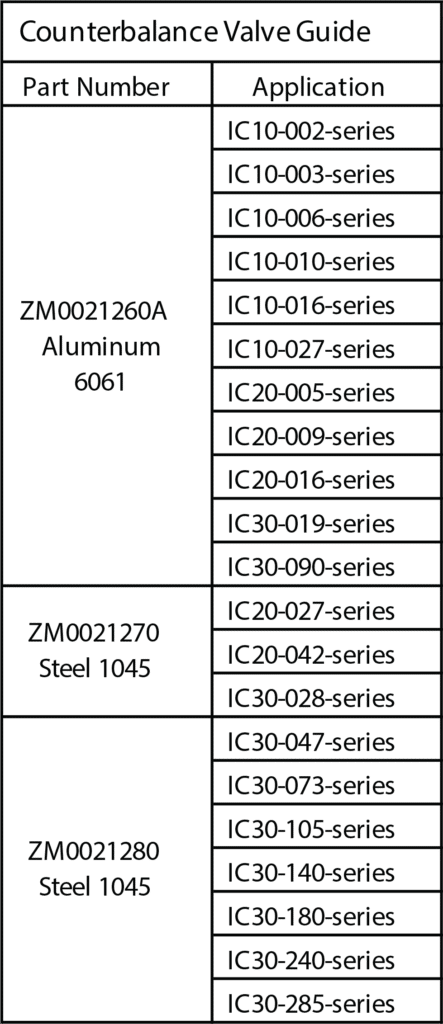
21260A Counterbalance Valve Block
Valve blocks are configured from aluminum and secured to a flat mounting pad on the actuator housing with three bolts. See each individual series page for specific valve locations. The pilot ratio is 3:1. The valves are set to relieve at 3,300 psi (228 bar).
21270 Counterbalance Valve Block
Valve blocks are configured from steel and secured to a flat mounting pad on the actuator housing with three bolts. See each individual series page for specific valve locations. The pilot ratio is 3:1. The valves are set to relieve at 3,300 psi (228 bar).
21280 Counterbalance Valve Block
Valve blocks are configured from steel and secured to a flat mounting pad on the actuator housing. Valve locations and plumbing routing differ among sizes. See each individual series page for specific valve locations. The pilot ratio is 3:1. The valves are set to relieve at 3,625 psi (228 bar).
Hydraulic rotary actuators are vital components in various industrial applications, often requiring precise control over heavy loads. To enhance the functionality and safety of these actuators, they can be accessorized with a counterbalance, or load-holding, valve. This option ensures the stability of the load by preventing unintended movement, especially in case of a hydraulic hose failure. By creating back pressure within the hydraulic line, these valves play a crucial role in controlling the load, thus averting any accidental movements of the actuator.
Often, the counterbalance valve is used as a safety device when the safety of humans is involved by protecting the actuator and thereby the person in case of a downstream hydraulic failure or by an upstream external force. Take, for example, a man lift where a person is in a basket. If there is hydraulic failure somewhere before the basket, the basket will stay in its place. If there is a force excerpted on the same basket if the operator hits an object while moving, the basket will rotate to protect its occupant.
Furthermore, due to the small oil volume (displacement) of the rotary actuator, temperature swings between night and day can cause substantial movement to whatever is mounted to the actuator if the actuator is not actuated. So, the counterbalance valve protects the actuator from overpressure applied to the actuator, or failure of a downstream component.
On some models, counterbalance valves can also be added to the system post purchase. This option provides a practical solution for those who may need to upgrade their existing system’s capabilities. Whether incorporated during the design stage or added later, these components can enhance the control, stability, and safety of hydraulic actuators across a wide range of industrial applications.
IC-Fluid Power, Inc. supports many applications including energy, marine & offshore, mining, packaging, plastic & injection molding, and more.